The method, purpose and significance of mineral processing
Author:WDY Magnetic Separator Release Time:2020-10-15 15:25:10 Views:
The ores mined from underground are generally composed of useful minerals and gangue, and their grade is generally relatively low, so they can not be directly smelted. Therefore, they need to be processed first to remove most of the gangue and harmful components, so that the useful minerals can be enriched into concentrate for further use. The process of separating useful minerals from gangue minerals by means of various mineral processing equipment according to their physical or chemical properties is called mineral processing.
What are the common mineral processing methods?
Common mineral processing methods: magnetic separation, gravity separation, flotation and electric separation.
Magnetic separation method is based on the different magnetic properties of minerals, so that different minerals in the magnetic field of the magnetic separator are subject to different forces, so as to obtain separation. It is mainly used for the separation of ferrous metal ores (iron, manganese, chromium); it is also used for the separation of nonferrous metal ores, rare metal ores and non-metallic minerals.
Gravity separation is based on the difference of mineral relative density (usually called specific gravity) to separate minerals. Mineral particles with different densities are affected by hydrodynamic and mechanical forces in the moving media (water, air and heavy liquid), resulting in suitable loose stratification and separation conditions, so that the mineral particles with different densities can be separated.
According to the difference of physical and chemical properties of mineral surface, the flotation method can make the useful minerals adhere to the bubbles selectively and achieve the purpose of separation. The mineral processing of nonferrous metals, such as copper, lead, zinc, sulfur and molybdenum, is mainly treated by flotation; some ferrous metals, rare metals and some non-metallic ores, such as graphite ore and apatite, are also processed by flotation.
The electric separation method is based on the difference of mineral conductivity. When the mineral passes through the high-voltage electric field of the electric separator, the electrostatic force acting on the mineral is different due to the different conductivity of the mineral, so the mineral can be separated. It is mainly used for the separation of rare metals, non-ferrous metals and non-metallic ores. At present, it is mainly used for separation and cleaning of mixed coarse concentrate, such as scheelite and cassiterite, zircon, tantalum and niobium ore.
What is the purpose and significance of mineral processing?
For example, wolframite ore generally contains a large amount of gangue, such as quartz, after beneficiation removes a large amount of gangue such as quartz, so that the tungsten mineral component is enriched and becomes a concentrate product. Some ores also contain elements harmful to the smelting process, such as sulfur and phosphorus in iron concentrates. Their content should not be too high, otherwise the pig iron will become brittle. Especially some multi-metal symbiosis ores, the metal components contained therein, such as Cu-Pb-Zn-Fe, are often harmful to each other during smelting, and only a variety of concentrate products obtained through beneficiation can be smelted separately. In addition, the technical and economic effects of beneficiation on smelting are also very obvious. For example, increasing the grade of copper concentrate from 15% to 16% can increase the smelting recovery rate by 0.1%~0.15%, and the production capacity by 6%~8%. Consumption is reduced by 6% to 7%; if the iron concentrate grade is increased by 1%, the blast furnace pig iron production will increase by 2.5% and the coke ratio will decrease by 1.5%.
Therefore, the purpose of mineral processing is to remove a large amount of gangue and harmful elements contained in the ore, so as to enrich the useful minerals, or separate the symbiotic useful minerals from each other, so as to obtain one or several useful concentrate products. Mineral processing is of great significance to the development of mining industry and the full utilization of mineral resources.
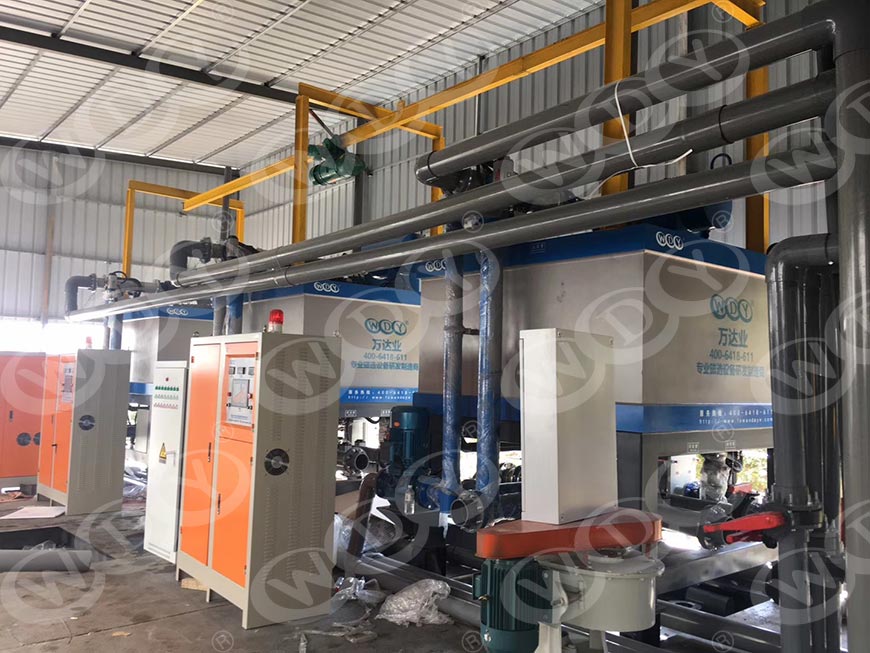
Common mineral processing methods: magnetic separation, gravity separation, flotation and electric separation.
Magnetic separation method is based on the different magnetic properties of minerals, so that different minerals in the magnetic field of the magnetic separator are subject to different forces, so as to obtain separation. It is mainly used for the separation of ferrous metal ores (iron, manganese, chromium); it is also used for the separation of nonferrous metal ores, rare metal ores and non-metallic minerals.
Gravity separation is based on the difference of mineral relative density (usually called specific gravity) to separate minerals. Mineral particles with different densities are affected by hydrodynamic and mechanical forces in the moving media (water, air and heavy liquid), resulting in suitable loose stratification and separation conditions, so that the mineral particles with different densities can be separated.
According to the difference of physical and chemical properties of mineral surface, the flotation method can make the useful minerals adhere to the bubbles selectively and achieve the purpose of separation. The mineral processing of nonferrous metals, such as copper, lead, zinc, sulfur and molybdenum, is mainly treated by flotation; some ferrous metals, rare metals and some non-metallic ores, such as graphite ore and apatite, are also processed by flotation.
The electric separation method is based on the difference of mineral conductivity. When the mineral passes through the high-voltage electric field of the electric separator, the electrostatic force acting on the mineral is different due to the different conductivity of the mineral, so the mineral can be separated. It is mainly used for the separation of rare metals, non-ferrous metals and non-metallic ores. At present, it is mainly used for separation and cleaning of mixed coarse concentrate, such as scheelite and cassiterite, zircon, tantalum and niobium ore.
What is the purpose and significance of mineral processing?
For example, wolframite ore generally contains a large amount of gangue, such as quartz, after beneficiation removes a large amount of gangue such as quartz, so that the tungsten mineral component is enriched and becomes a concentrate product. Some ores also contain elements harmful to the smelting process, such as sulfur and phosphorus in iron concentrates. Their content should not be too high, otherwise the pig iron will become brittle. Especially some multi-metal symbiosis ores, the metal components contained therein, such as Cu-Pb-Zn-Fe, are often harmful to each other during smelting, and only a variety of concentrate products obtained through beneficiation can be smelted separately. In addition, the technical and economic effects of beneficiation on smelting are also very obvious. For example, increasing the grade of copper concentrate from 15% to 16% can increase the smelting recovery rate by 0.1%~0.15%, and the production capacity by 6%~8%. Consumption is reduced by 6% to 7%; if the iron concentrate grade is increased by 1%, the blast furnace pig iron production will increase by 2.5% and the coke ratio will decrease by 1.5%.
Therefore, the purpose of mineral processing is to remove a large amount of gangue and harmful elements contained in the ore, so as to enrich the useful minerals, or separate the symbiotic useful minerals from each other, so as to obtain one or several useful concentrate products. Mineral processing is of great significance to the development of mining industry and the full utilization of mineral resources.
Related Articles
PREV:A brief analysis of kaolin iron removal process
NEXT:Application range of dry magnetic separators
YOU MAY ALSO LIKE...